Pac Composites > Services > Preformers & Hot Drape Formers
Preformers & Hot Drape Formers
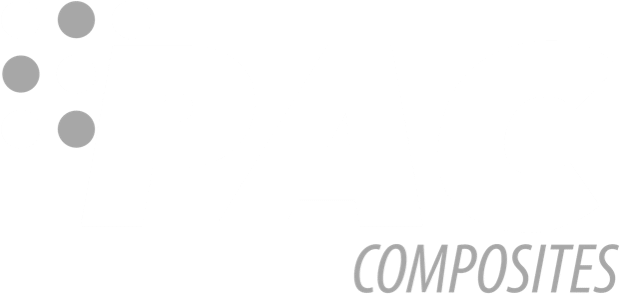
Preformers & Hot Drape Formers Northern Ireland
About Preformers & Hot Drape Formers
We are one of the leading specialists in the design and manufacture of Hot Drape Forming Machines for use by companies operating in the Aerospace, Marine and Automotive industries.
At PAC Group, we understand that the quality of each manufactured part is dependent on the quality of the machine in which it is formed. This is why we put the highest level of monitoring and control into our machines, to produce parts of exceptional quality.
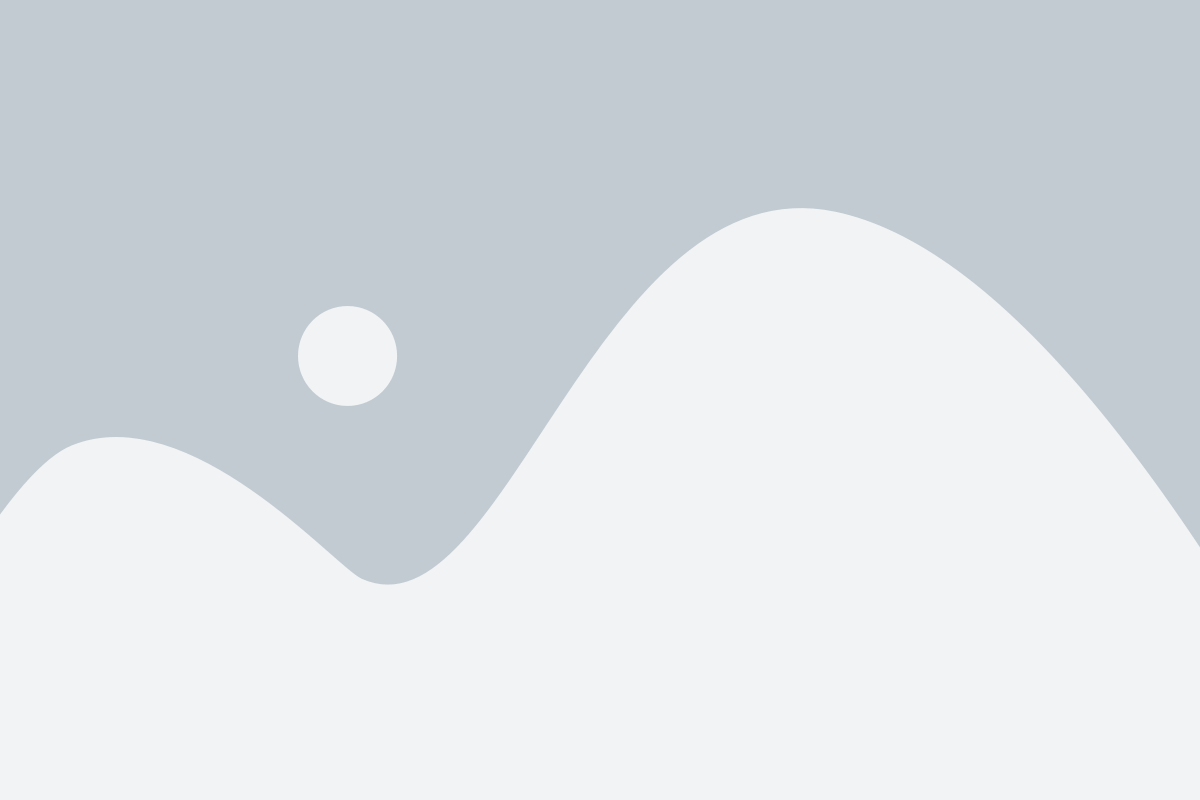
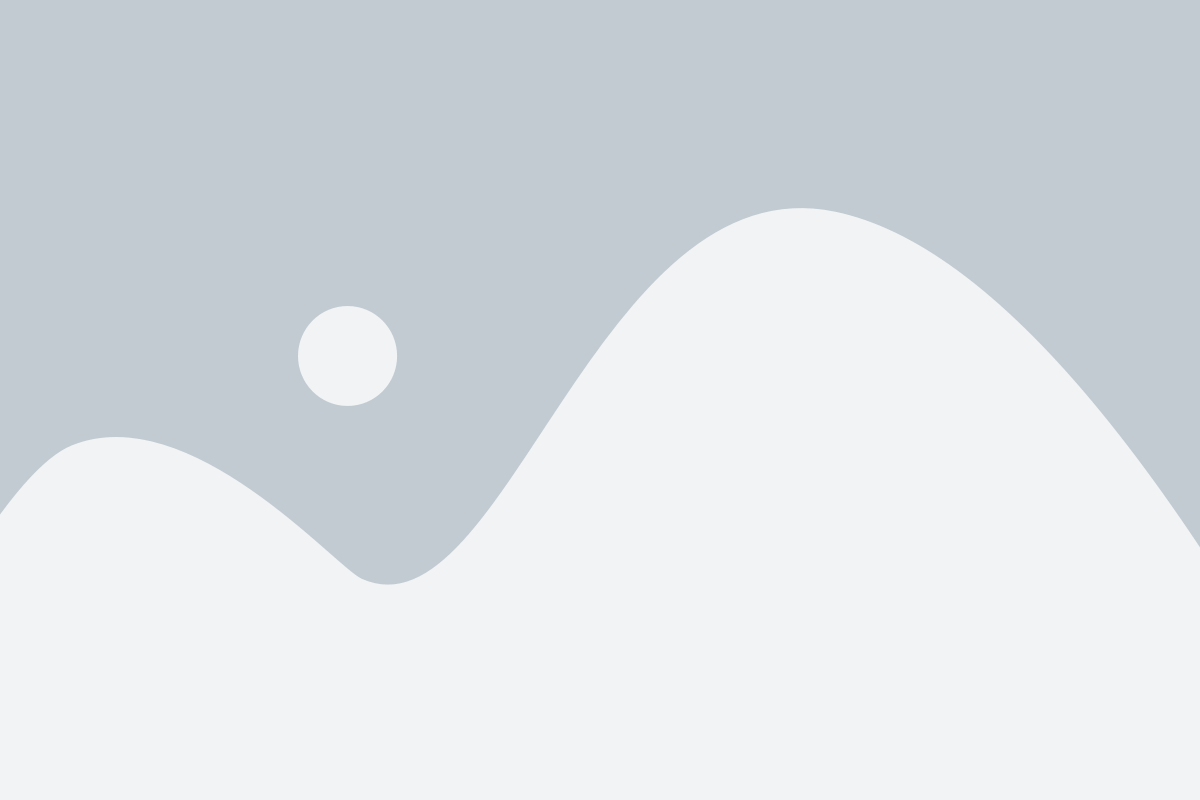
Tool Control
To help with temperature uniformity of complex parts, a tool control option is available. This specially-designed software algorithm takes into account Thermal Uniformity Survey (TUS) information and will monitor tool thermocouples to automatically adjust machine set-points.
Pneumatic Diaphragm
For machines with fixed tables, or that require operators to work on the part in the working area of the forming machine, a pneumatic diaphragm option is available. This system raises
the diaphragm up to the lower face of the hood and locks it in place, allowing additional head room for operator access.
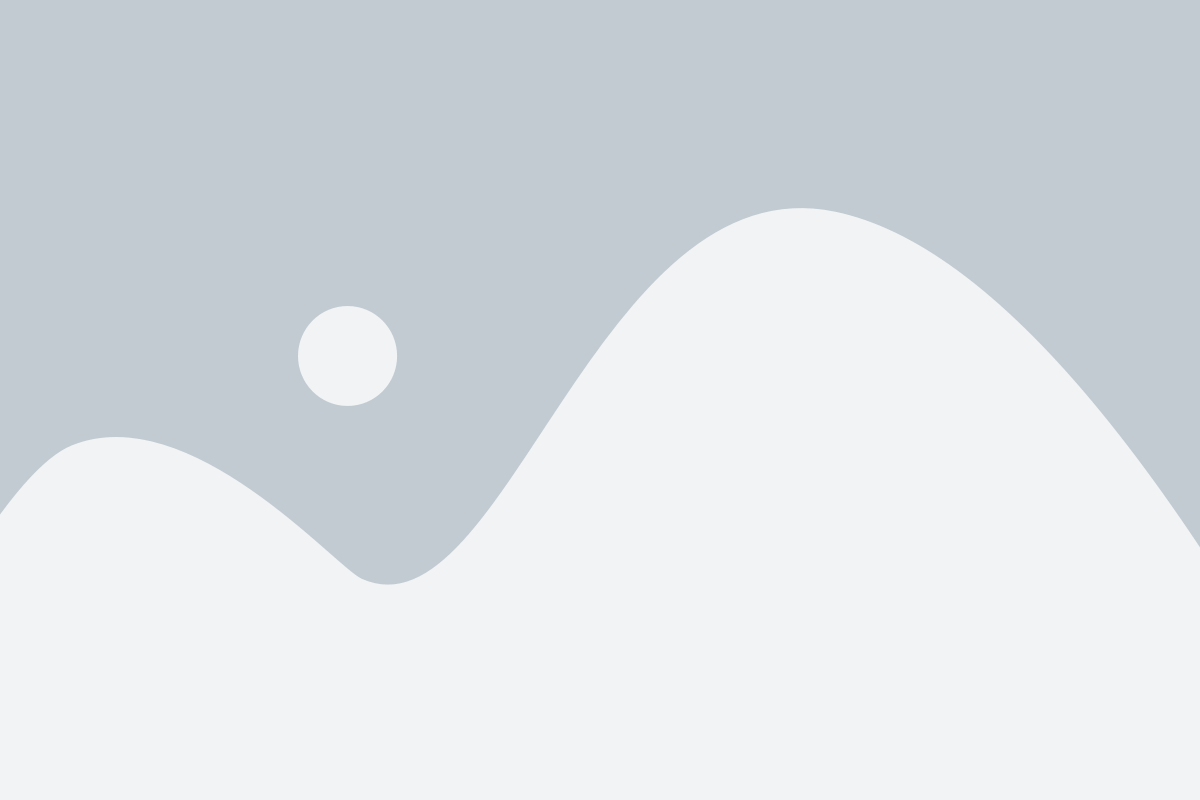
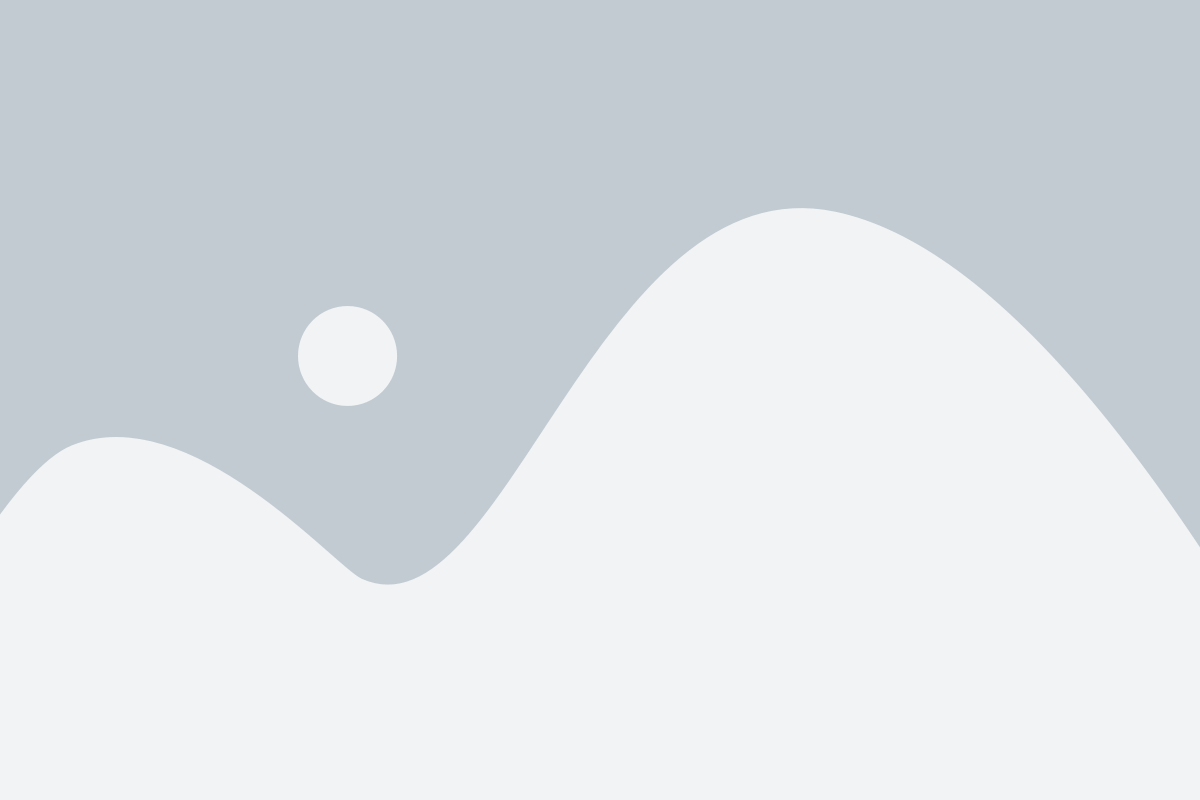
Bespoke Designs
We pride ourselves on being able to create bespoke and custom designs to suit your every requirement.
Our machines can be supplied with or without a fixed table or removable trolly to suit the application. We can manufacture a machine of any size within the structural limitations of 30 metres long by six metres wide.
Heater Angle Positioning And Forced Cooling
To help reduce cycle time, we offer a recipe-controlled heater angle positioning system. This system controls the angle of the heaters via positional motors to direct the heat to give the best possible ramp-up temperature rate and heat penetration into the part.
To help further reduce cycle time, our forced cooling system is designed to direct cool air into the preforming working zone at the end of the cycle. This greatly reduces the cool-down time required between machine cycles.
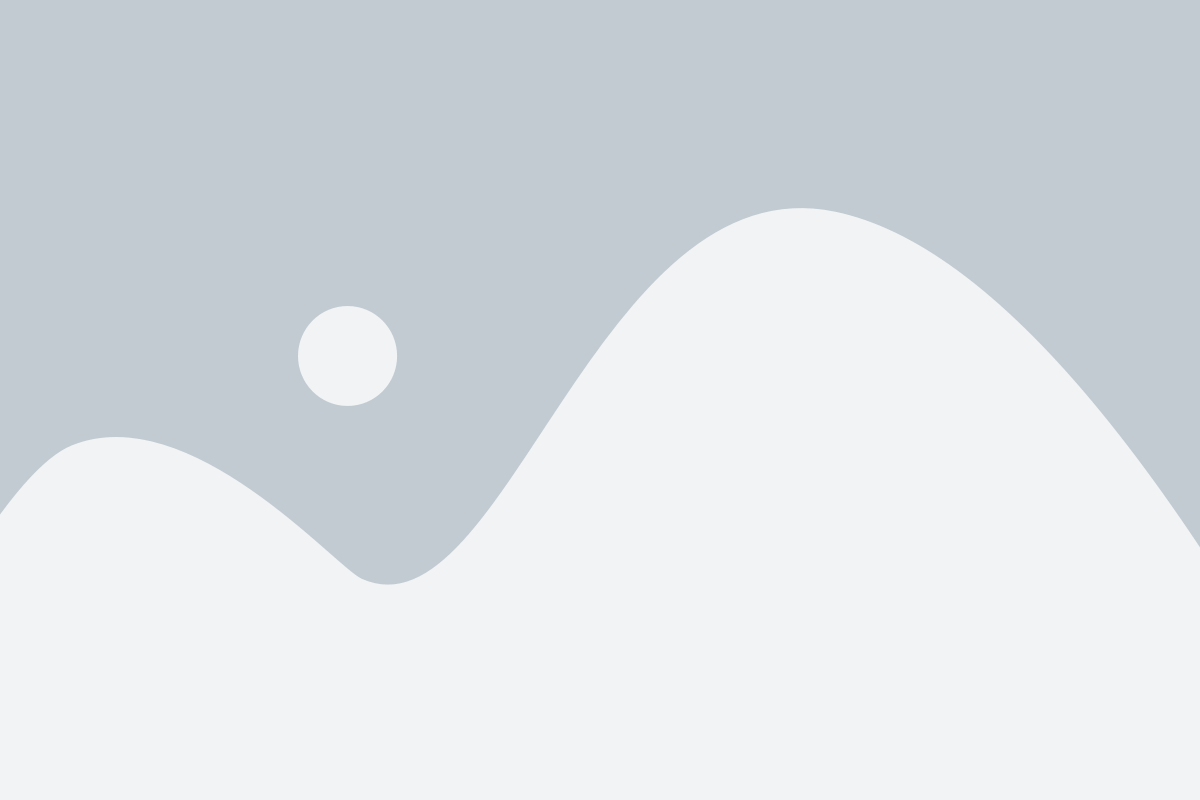
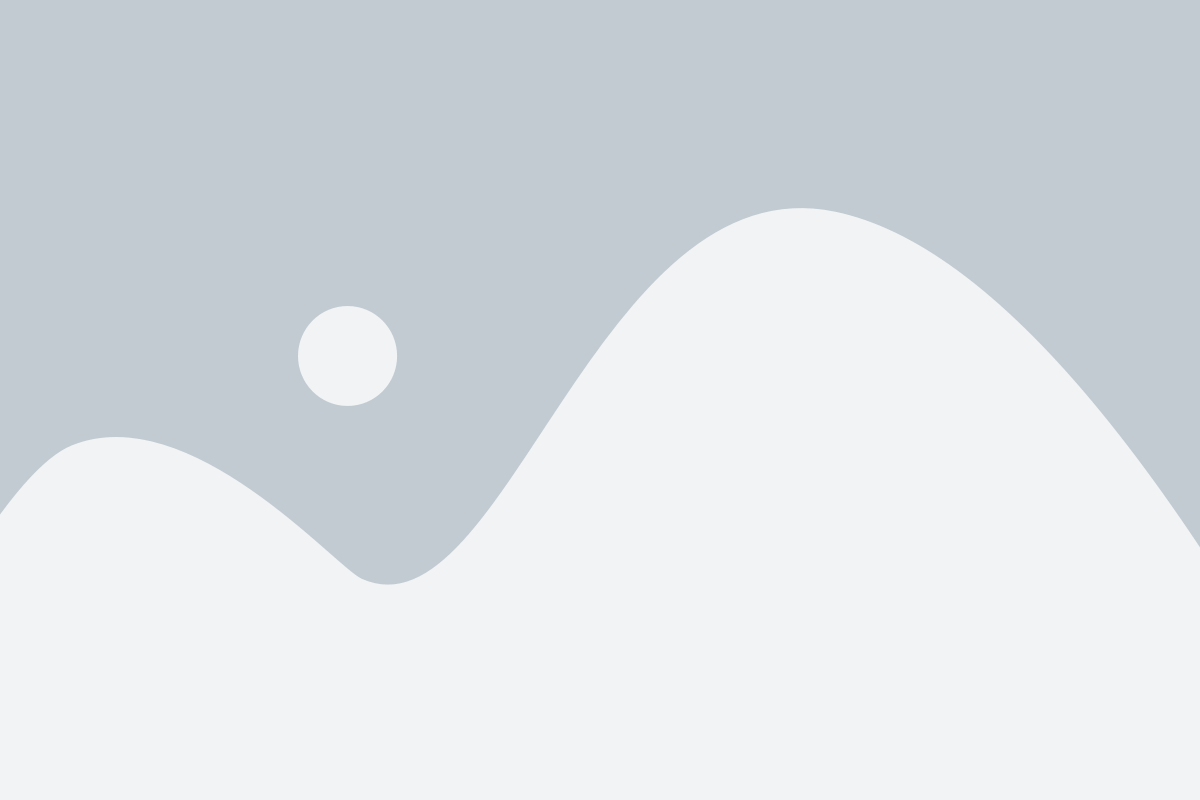
Control Panel Location
Unlike other manufacturers, we locate all of the advanced hardware in a bespoke master control panel located away from the moving parts of the machine. This can reduce downtime and assist with maintenance by allowing easy access to critical components. Our standard machines allow for the control panel to be located adjacent to the machine. However, other options are available.
The PAC team can integrate controls into the machine where possible to reduce overall factory floor footprint.
Operator Interface
Our standard operator interface, via a colour touchscreen, allows for the configuration, storage and retrieval of recipes while data logging is performed by a graphic recorder.
Records can be accessed via the recorder touchscreen, exported, or downloaded to USB.
A more advanced Computer Controlled SCADA system is also available.
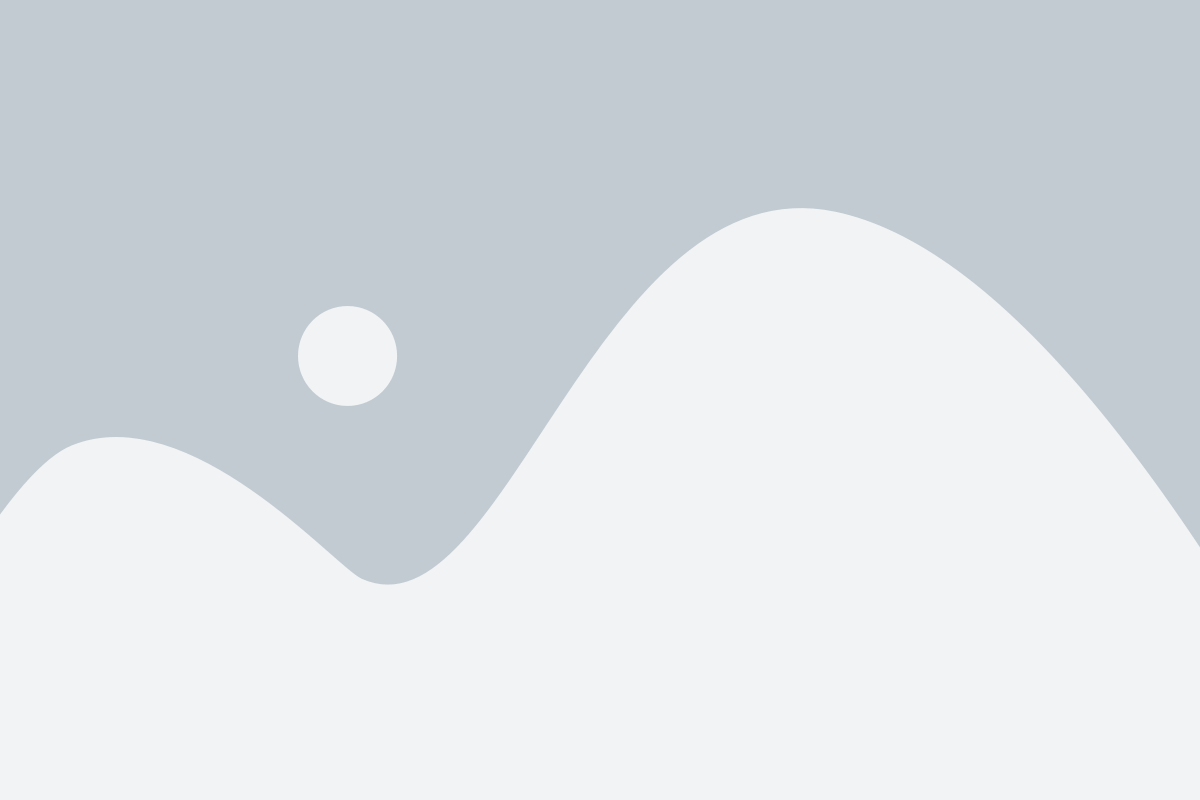
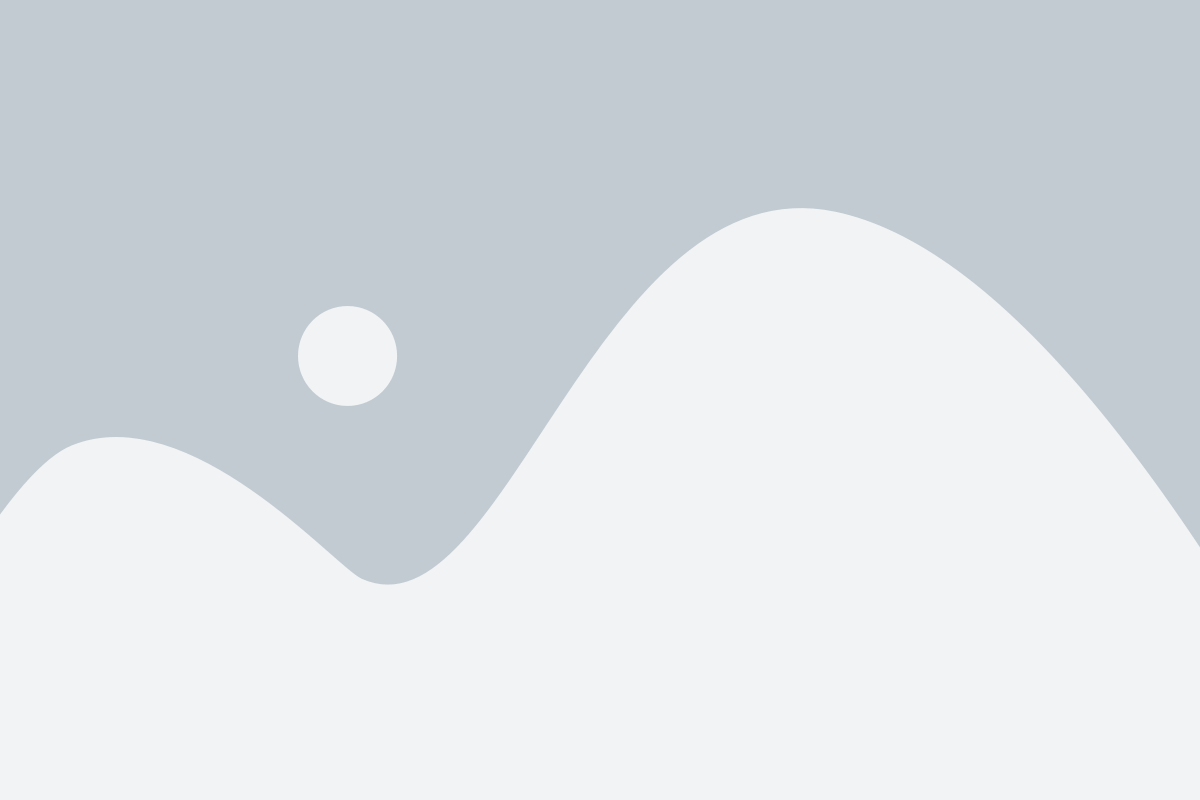
TUS Pack
To assist Quality Engineers in Thermal Uniformity Surveying, we have developed unique options to simplify and speed up the process. We offer both standard and advanced options, depending on your requirements. OVER-TEMPERATURE PROTECTION To comply with NADCAP requirements we offer an independent over- temperature protection option.
Maintenance Pack
We know that the first line of defence in avoiding downtime is the on- site maintenance team. To combat that, we offer a comprehensive maintenance pack, which includes:
- One week of training at our facility or on the client’s site for up to five client engineers (excludes travel and accommodation).
- A fully configured maintenance laptop with pre-loaded diagnostics software.
- On-going technical support and guidance, as required by the client, which can include bespoke packages to cover remote assistance, regular visits and on-site support.
Holding 42 patents on the hardware and software, we have designed & built preformers for some of the biggest names in the aerospace & automotive sectors including Bombardier, McLaren, Spirit Aerosystems and Aerospace Innovation Centre.
Whatever your project, we’re here to help. Speak with our expert Engineers today to see how we can design & build a machine for your exact requirements. Get in touch by emailing info@pacgroup.co.uk.
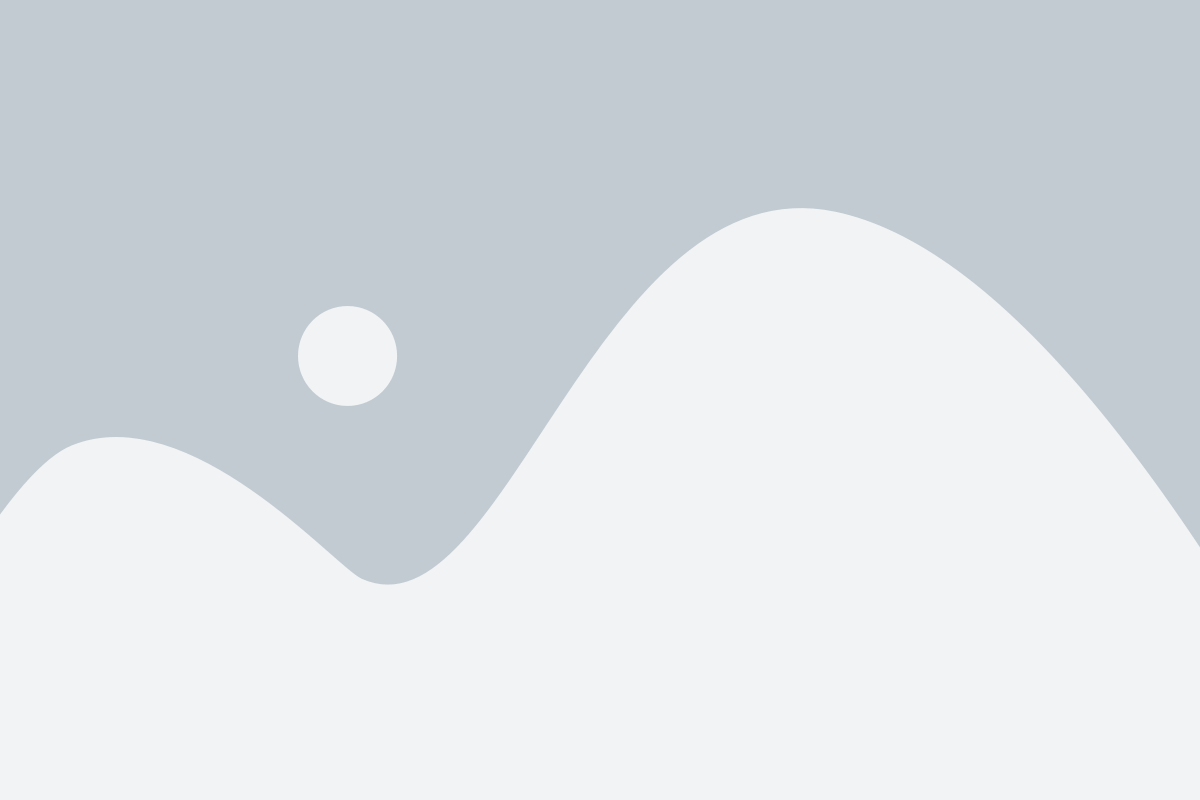